Six Flags America
Largo, Maryland
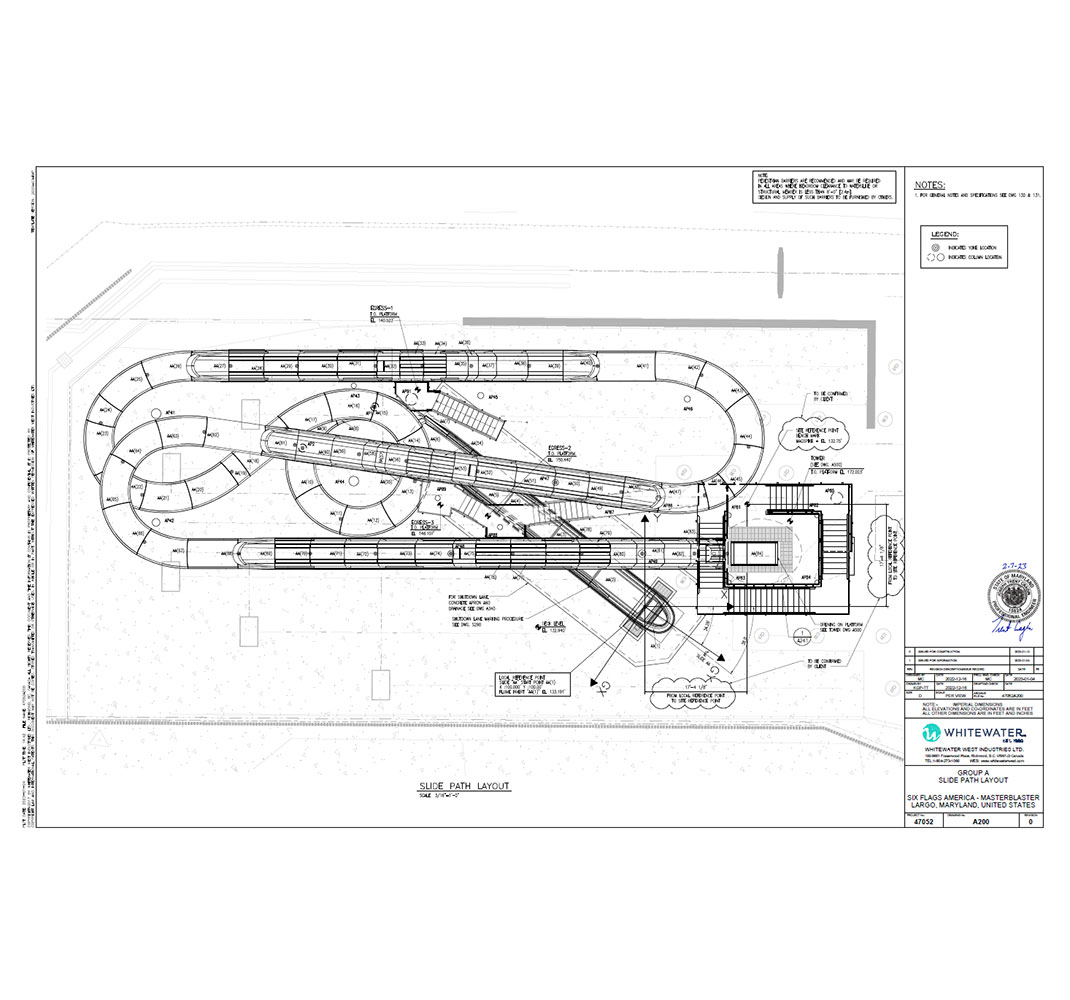
Six Flags America unveils the spectacular RipQurl Blaster water attraction, engineered by JPG's commercial plumbing pros!
Challenge
In the summer of 2023, Six Flags America in Largo, Maryland, debuted their latest attraction, the RipQurl Blaster, the region’s tallest “Master Blaster Water Coaster,” and the park’s largest capital investment in over a decade. RipQurl Blaster is an innovative water coaster taking riders in a raft through three powerful uphill rip currents while zigzagging through 550 feet of twists and turns. The ride features three breathtaking drops, three AquaLucent hairpin turns, and a pitch-black wall-hugging helix finale before the final splashdown.
With such a large investment on the line, Six Flags needed to ensure that the new attraction was a refreshing and fun ride for the park’s thrill-seekers—and because it is a water ride, that its plumbing functionality operated safely and efficiently.
With JPG Services having performed VAC services work at Six Flags America prior to the Covid-19 pandemic, the operations staff at Six Flags was already impressed with the professionalism and customer service JPG technicians provided. JPG was asked to bid on the plumbing work for their new water coaster—and after walking the project and studying the plans and requirements, we submitted a bid to deliver an efficient and economical design to the project. Our detailed bid, as well as our extensive experience, expertise, and knowledge of complex commercial plumbing challenges, was the winning formula to be hired.
Solution
JPG technicians worked closely with park engineers and Six Flags staff to design a system that tied the new water attraction back to the park’s existing pump system, and to find the most effective products and procedures so that park patrons were not disturbed during the construction of the attraction and the attraction’s infrastructure. Working with the team at Six Flags, JPG ensured that the placement of our plumbing did not interfere with staff’s daily duties or customer traffic and flow.
Results
JPG’s ability to work with the project’s engineering firm, as well as the Six Flags team, opened up lines of communication that helped JPG technicians to be more efficient with the project work. This open communication also helped JPG to move faster and gave them a clear scope of where the pumps, meters, and valves needed to be located, making it easier to check the valves and meters when the ride was being used on a daily basis.
← Return to Projects